TPM Nedir?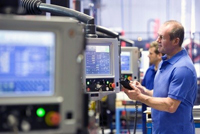
Toplam Verimli Bakım ya da kısaca bilinen adıyla TPM (Total Productive Maintenance) üretim sistemlerinde sıfır ekipman duruşu ve sıfır kalite hatası hedefleyen bir bakım sistemidir.
TPM, üretim ve hizmet süreçlerinde, tüm çalışanların katılımını gerektiren, otonom bakımı öngören, arıza giderme değil önleme yaklaşımını benimseyen, ekipman etkinliğini en üst düzeye getiren bir bakım yönetimi yaklaşımıdır.
TPM Yaklaşımı Nedir?
- Süreçlerin etkinliğini maksimize edecek şekilde bir şirket kültürü oluşturur.
- Toplam sistem mevcut ekipman ve üretim alanı ile ilgili kayıpları önleyen ve 5 “sıfır” (kaza, arıza, küçük duruş, hata, hurda) hedefine ulaşacak kusursuz bir sistem kurar.
- TPM grup çalışmasıdır, organizasyonun tüm birimlerini ve tüm bireylerini içerir İşletmede bulunan tüm departmanlar tarafından uygulanır. En yüksek kademeden en alt kademeye kadar herkesin katılımı ile gerçekleştirilir.
- TPM Küçük grup faaliyetlerine dayanır. Otonom Bakım faaliyetleri ve Kaizen aktiviteleri ile “sıfır kayıp” hedefine ulaşır.
TPM’in Hedefleri Nedir?
- Rekabet gücünü arttırmak.
- Kolay çalışılan yüksek performanslı bir is yeri yaratmak.
- İşletme bazında bakım yapmaya aktif katılımı sağlamak.
- İstikrarlı ürün kalitesini sağlamak.
- İstikrarlı ürün teslimatını sağlamak.
- Kayıpları yok ederek yüksek kârlılığa ulaşmak.
- Çalışma ortamına canlılık getirmek ve iş güvenliğini sağlamak
En Temel Faydaları Nedir?
- Üretim sisteminin verimliliğini en üst düzeye çıkaracak bir şirket kültürü oluşturur.
- Mevcut ekipman ve üretim alanı ile ilgili her türlü kaybı (arıza, iş kazası, kalite hatası… vb.) önleyecek kusursuz bir sistem kurar.
- Yalnızca üretimle ilgili departmanlarda değil tüm birimlerde uygulanır.
- Otonom bakım ve küçük grup faaliyetleri ile “sıfır kaybı” ön görür
Üretim Kayıpları Nelerdir?
Günümüzde rekabet gücünü belirleyen en önemli faktörler:
- Kalite,
- Maliyet,
- Hız (Müşterinin istediği zamanda teslimat)
Kaliteyi artırırken maliyeti düşürebilmek ve verimliliği sağlayabilmek için 16 büyük kaybın yok edilmesi gereklidir.
Ekipman etkinliğini etkileyen 8 kayıp:
- Arıza
- Set-up ayar ( model değişimi)
- Takım değişimi
- Başlangıç
- Küçük duruş ve boşta bekleme
- Hız
- Hata ve tamir
- Kapatma
İş gücü etkinliğini etkileyen 5 kayıp:
- Yönetim
- Üretim hareket
- Hat organizasyon
- Lojistik
- Ölçme ve ayar
Malzeme ve enerji etkinliğini etkileyen 3 kayıp:
- Enerji
- Ürün
- Ekipman( kalıp ve el aletleri)
Kaizen Nedir?
Ekipman, işçilik, malzeme ve enerji etkinliğinin sağlanması için 16 büyük kaybın yok edilmesine yönelik yapılan çalışmalardır. Bunun dışında tertip düzen,iş güvenliği ve çevreye yönelik olumsuzlukların iyileştirilmesi çalışmalarınıda kapsar. Temelde amaç Mudaları “İsraf” yok etmektir.
Kaizen ve yenilik kavramları birbirine karıştırılmamalıdır. Yenilik, büyük yatırımlar ve teknolojik değişikliklerle sıçrama yaparak performans iyileştirmeleri yapmaktır. Kaizen ise m
evcut üretim sisteminizde yukarıda da bahsedilen kayıpların tek tek ele alınarak çözülmesi anlamına gelir. İşletmeler için iki kavramda gereklidir ancak yenilikler ancak kaizen ile birlikte anlamlı olur.
Cost Loss Matrisi Nedir?
Cost loss matrisi, işletme içerisinde tespit edilen 16 büyük kaybın “Bu sayı işletmelerde farklılık gösterebilir” makine, işçilik, malzeme, enerji ve stoklar başlıkları altında gruplanarak
bir tablo üzerinde katma değerli ve katma değersiz olarak rakamlar üzerinden ifade edilmesidir.
Cost loss matrisleri her sene sonunda yapılarak bir sonraki yıl için kaizen konuları belirlenir ve diğer TPM pillarlarına sayısal getiri hedefleri verilir. Cost loss matrisi işletme kayıplarının bir arada görülebildiği ve kaizen yol haritası olma özelliğiyle etkili bir yöntemdir.
Kaizen Türleri
Kaizen ekip üyeleri iyileştirilecek konuya göre seçilirler. Hızlı yol almak ve doğru sonuca ulaşmak için bu şarttır. Temelde anlam kargaşasına yol açmamak için iki çeşit kaizen vardır diyebiliriz. Bunlar;
a) Önce Sonra Kaizen (Before – After)
- Birey öncelikli çalışmalardır.
- Ekip sayısı en fazla 2 kişi olmalıdır.
- Tecrübe ve sağduyu ile gerçekleşir.
- Her an uygulanır.
- Tüm alanlarda uygulanır.
- Kısa sürede tamamlanan çalışmalardır.
b) Kobetsu Kaizen
- Ekip öncelikli çalışmalardır
- Veri takibi gerektirir
- Uzun süreli çalışmalardır
- Öncesinde ve sonrasında gözlem ve izleme gerektirir.
- Ekip en fazla 5 en az 3 kişiden oluşabilir.
- 16 büyük kaybı içerir. (İşletme kayıp adetleri değişiklik gösterebilir)
TPM Ödülü Alan 250 Fabrikanın Sonuçları Ortalaması
- % 50 Prodüktivite Artışı
- % 99 Makine Arızalarında Azalma
- % 90 Ürün Hatalarındaki Azalma
- % 75 Müşteri Şikayetlerinde Azalma
- % 30 Bakım Maliyetinde Azalma
- % 50 Yarımamul Stoklarındaki Azalma
- % 30 Enerji Kullanımındaki Azalma
- İş Kazalarındaki Azalma (Sıfır Kaza)
- Çevre Kirliliğindeki Azalma (Sıfır Kirlilik)
- İşçi Önerilerindeki Artış (10 Kat)
TPM’ in Ölçülemeyen Sonuçları
- Otonom bakım çalışmalarının bir sonucu olarak çalışanlar makinelerine sahip çıkmaya başlıyor.
- ‘Sıfır Kusur’ , ‘Sıfır Arıza’ , ‘Sıfır Kaza’ inancı yaygınlaşıyor.
- Çalışma ortamı daha temiz, daha düzenli bir hale geliyor.
- Bölümler arası işbirliği artıyor.
- Bilgi paylaşımı ve aktarımı yaygınlaşıyor.
- Değişime olan direnç kalkıyor.
TPM Uygulama Aşamaları
- TPM Uygulanacağının İlanı
- TPM Konusunda Tanıtım ve Eğitim Faaliyetinin Başlatılması
- “TPM Ofisi” nin Oluşturulması
- TPM Konusunda Hedef, ve Politikaların Belirlenmesi
- Master Plan ve Organizasyonun Hazırlanması
- TPM Başlama Vuruşu (Kick – off)
- Üretim Verimliliğini Arttırıcı Sistemlerin Kuruluşu
- Yeni Makina ve Techizat / Yeni Ürün Devreye Alma Yeteneklerin Geliştirilmesi
- Kalite Bakım “Hinshitsu-hozen” Sisteminin Kurulması
- Ofis TPM: TPM’i Endirekt İşlerde ve Ofiste Uygulamak
- Hijyen, İşçi Sağlığı ve İş Güvenliği, Çevre Koruma Konularında TPM
- TPM’in Tam Uygulanması TPM ÖDÜLÜ için BAŞVURU !
Çalışanlar TPM in neresinde?
TPM çalışanları ve ekipmanı geliştirerek şirket kültürünü değiştirmeyi amaçlar.Çalışanlar eğitim ve sorumluluk vererek geliştirilir. Bunu yapabilmek için, her kademedeki çalışanın yeteneklerinin arttırılması gerekir.
- Operatörler (otonom bakım yeteneği geliştirilir),
- Bakım personeli (yüksek kalitede bakım yeteneği geliştirilir),
- Mühendisler (ekonomik, kullanıcı dostu ve bakım gerektirmeyecek ekipman ve ürünler tasarlama yeteneği geliştirilir).
Çalışanlar geliştirilirken ekipman da geliştirilir. Ekipman performansı arttırılarak etkinlik arttırılır. Yeni ekipman tasarımlarında LCC ( Life Cycle Cost ) düşüncesi oluşturulur ve başlangıç zamanı kısaltılır.
TPM Gelişiminin 5 Prensibi
- Etkin üretkenliğin sağlanması için sistem kurulması
Kobetsu Kaizen
Otonom Bakım
Planlı Bakım
Eğitim - Yeni urun ve ekipman için akış kontrol sisteminin kurulması (Erken urun/ekipman yönetimi)
- Kalitede bakım sisteminin kurulması (Kalite Bakım)
- Ofis TPM
- İş güvenliği ve Çevre
TPM faaliyetleri sadece ekipman ile ilgili kişiler tarafından değil ilişkili tüm departman çalışanları tarafından yapılmalıdır. Yapılacak çalışmalar tüm ekip çalışanları tarafından paylaşılmalıdır.
TPM Uygulamalarına Nasıl Başlamalı
- Üst Yönetimin TPM başlangıç deklarasyonu
- Tüm çalışanlara başlangıç eğitimi verilmesi
- TPM hedeflerinin belirlenmesi
- Faaliyet planın hazırlanması
- Pilot uygulamaların yapılması
- Pillarların kurulması
- TPM faaliyetlerin tüm fabrikaya yaygınlaştırılması